Utilizing 3D Coldspray Printing Technology for Techno-G Valve Production!
tim2023-09-21T09:15:13+00:00The current Techno-G Ball Segment Valve is traditionally manufactured using either Stainless Steel or a type of Hastelloy due to its exceptional corrosion resistance and wear resistance properties.
However, employing Hastelloy is both labor-intensive and significantly pricier than Stainless Steel. In light of this, Techno-G has embarked on a quest to explore the possibilities of using corrosion-resistant and wear-resistant materials within the realm of 3D production technology.
Thus, the Techno-G development team initiated research into whether the components of a Techno-G Ball Segment Valve could be 3D printed using the 3D metal Coldspray process while meeting the same material requirements as those in conventional Ball Segment Valve production.
The 3D Coldspray printing process, utilizing Titanium as the base material, has already undergone extensive research and experimentation. With this wealth of experience, the Techno-G design team reimagined the body design of the Techno-G Ball Segment Valve to adapt it for use in the 3D Coldspray printing process. Presently, the initial results, as depicted in the images, are highly promising!
Here’s a summary of the key benefits of the 3D printing process:
- Reduced lead times
- Decreased raw material usage
- Enhanced design flexibility
- Lower production costs
In conclusion, there are ample possibilities for various components of the Techno-G Ball Segment Valve to be produced using 3D Coldspray Printing technology in the future.
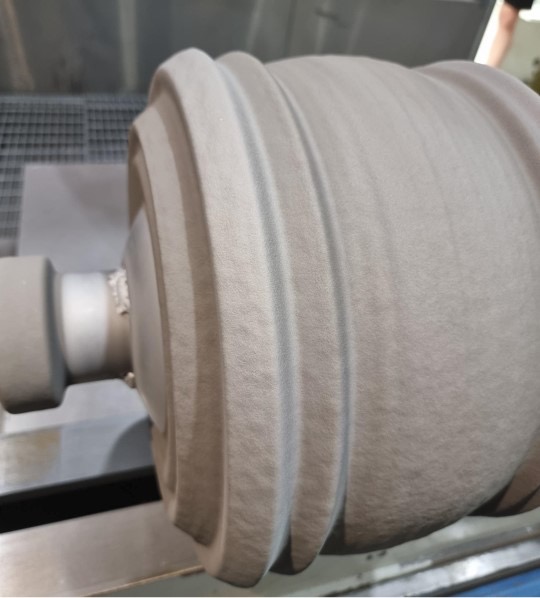
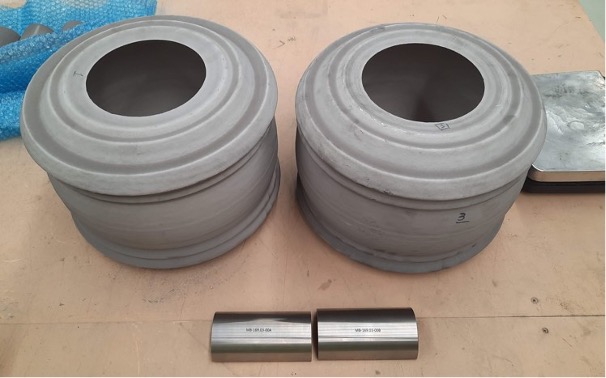
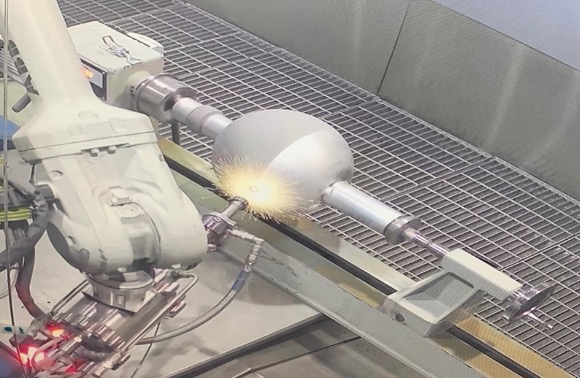
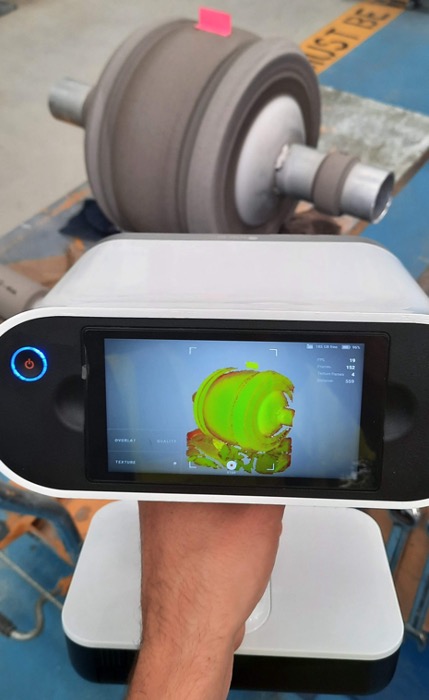
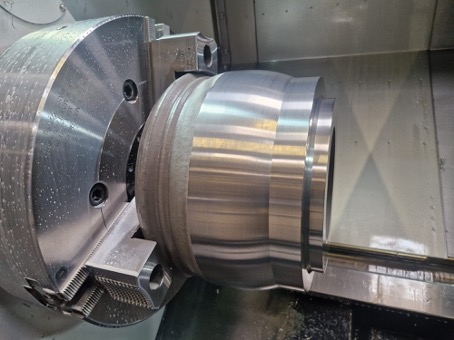