Exploring 3D Printing for Ball Segment Valves: Techno-G’s Innovations
tim2023-10-11T13:01:18+00:00Techno-G Ball Segment Valve is typically produced using either Stainless Steel or a specific variant of Hastelloy, which is distinguished by its remarkable resistance to corrosion and wear.
In light of the cost and labor-intensive nature of employing Hastelloy, Techno-G undertook an adventure to explore the potential of utilizing corrosion-resistant and wear-resistant materials within the field of 3D production technology.
The Techno-G development team initiated research to determine if the components of a Techno-G Ball Segment Valve could be manufactured using the 3D metal Cold spray process, while still meeting the same material specifications as those used in conventional Ball Segment Valve production.
Extensive research and experimentation have been conducted on the 3D Cold spray printing process, which utilizes Titanium as its core material. Building upon this knowledge, the Techno-G design team redesigned the body of the Techno-G Ball Segment Valve to ensure its compatibility with the 3D Cold spray printing process.
Key benefits arising from utilizing 3D printing process:
- Reduced lead times
- Decreased raw material usage
- Enhanced design flexibility
- Lower production costs
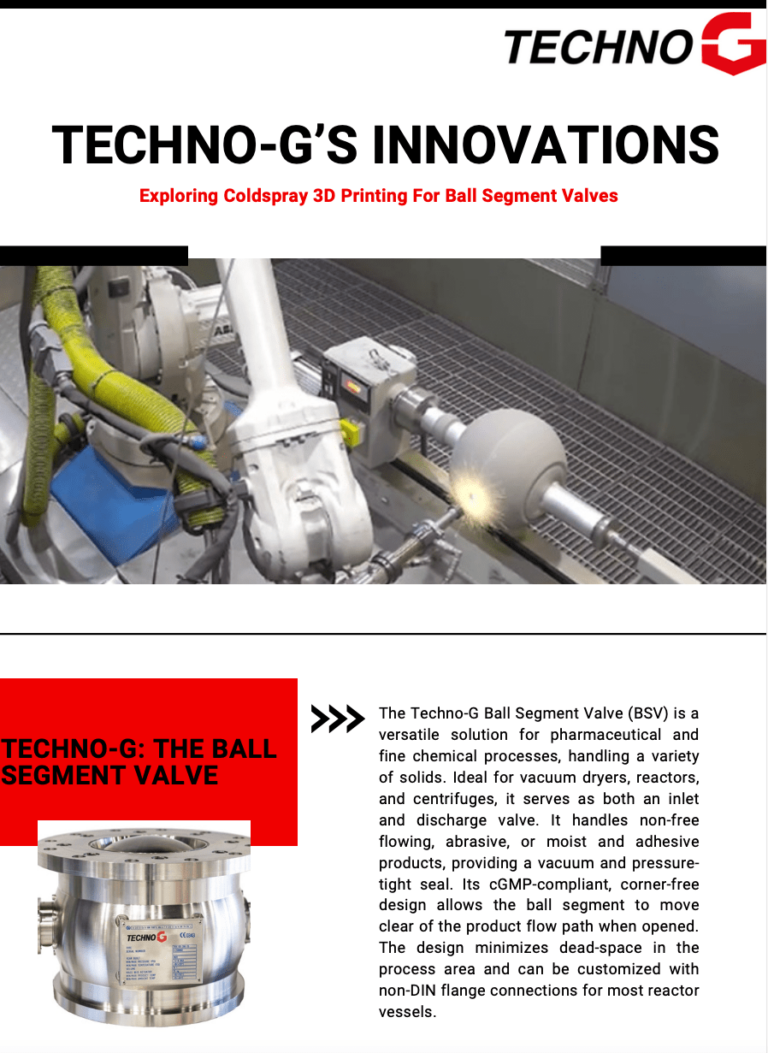
Download our free whitepaper
"Exploring Coldspray 3D Printing For Ball Segment Valves"
The Techno-G Ball Segment Valve (BSV) is a versatile solution for pharmaceutical and fine chemical processes, handling a variety of solids. Ideal for vacuum dryers, reactors, and centrifuges, it serves as both an inlet and discharge valve. It handles non-free flowing, abrasive, or moist and adhesive products, providing a vacuum and pressure- tight seal. Its cGMP-compliant, corner-free design allows the ball segment to move clear of the product flow path when opened. The design minimizes dead-space in the process area and can be customized with non-DIN flange connections for most reactor vessels.
The Techno-G Ball Segment Valve (BSV) is a versatile solution for pharmaceutical and fine chemical processes, handling a variety of solids. Ideal for vacuum dryers, reactors, and centrifuges, it serves as both an inlet and discharge valve. Learn more.
Cold Spray 3D printing with a gas stream process
Cold spray 3D printing with a gas stream is an innovative additive manufacturing process that utilizes high-velocity gas to build 3D objects layer by layer. Unlike traditional 3D printing methods that rely on melting and solidifying material, this approach operates at relatively low temperatures.
Step by step approach:
- Material Selection: The process typically employs metal or metal alloy powders as the raw material. The choice of powder depends on the desired properties of the final object, such as strength, conductivity, or corrosion resistance.
- Gas Stream Propulsion: Instead of using high-velocity particles, this method employs a high-speed, often heated, gas stream, such as compressed air or nitrogen. The gas stream acts as the propellant for the metal powder.
- Material Deposition: The gas stream carries the selected metal powder and directs it onto the substrate or workpiece. As the particles make contact with the surface, they undergo plastic deformation and form strong metallurgical bonds with the underlying material.
- Layer-by-Layer Assembly: A computer-controlled system or robotic arm guides the gas stream nozzle to deposit the metal powder in a predefined pattern, building up the 3D object layer by layer.
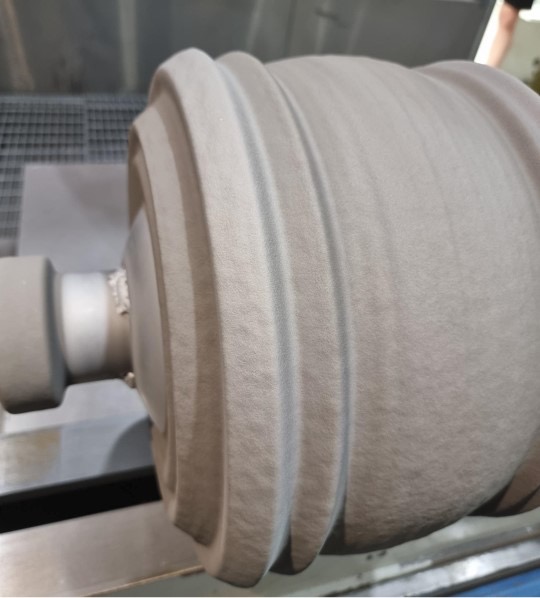
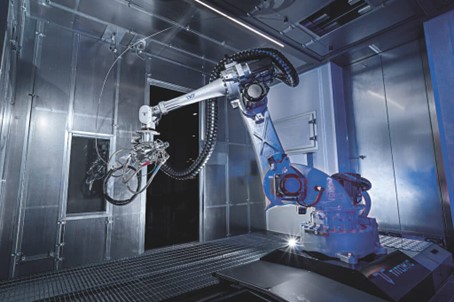
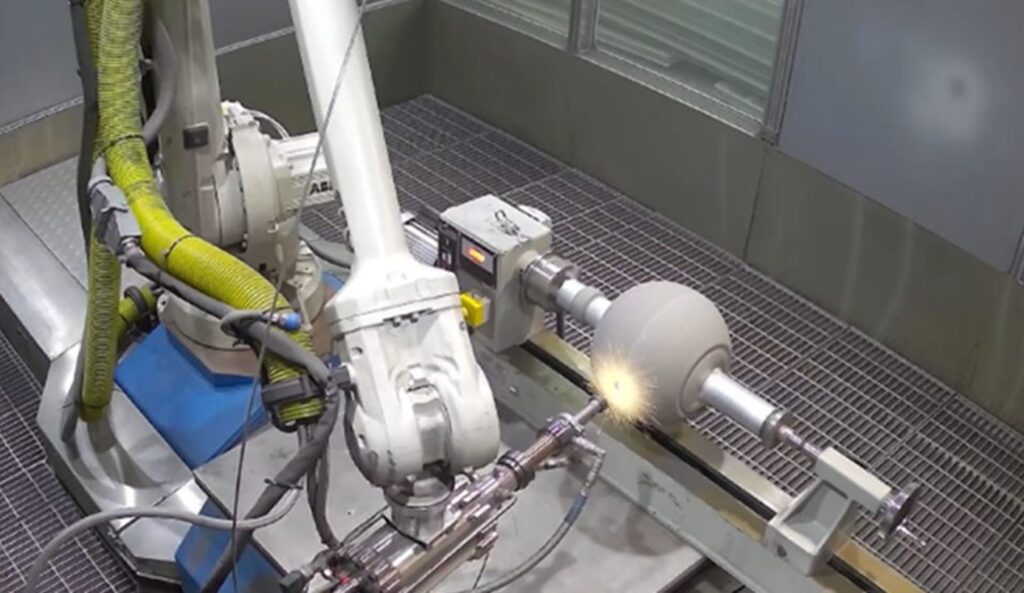