Techno-G has a unique CIP cover for the entire Ball Segment Valve Range!
Techno-G2024-11-20T15:23:59+00:00Techno-G always opts for a “rotating CIP head” because it provides complete coverage within the entire housing and effectively reaches even the dead corners.
Cleaning in Place (CIP) in the Pharmaceutical Industry:
CIP is a process used to clean equipment and pipeline systems without disassembly. In the pharmaceutical industry, it is critical for ensuring consistent, thorough, and reproducible cleaning of production equipment while adhering to strict hygiene standards.
How Does CIP Work with Liquid Cleaning?
- Automation: The process is usually fully automated to minimize manual intervention, reducing the risk of human error.
- Cleaning Stages:
- Water Rinse: Pre-cleaning to remove loose debris and residues, often using warm water.
- Cleaning with Detergent: An alkaline or acidic cleaning agent is pumped through the equipment to remove stubborn contaminants such as proteins or minerals.
- Water Rinse: Residual cleaning agents are flushed out using demineralized or pure water.
- Disinfection (optional): A disinfectant may be used in sensitive processes to eliminate microbial contamination.
- Final Rinse: A last rinse with sterile or purified water ensures the system is left clean.
- Use of Liquids:
- Cleaning Agents: Specific chemicals such as caustic soda (NaOH) or acids like phosphoric acid are selected based on the type of contamination.
- Water Quality: The industry uses water grades like Purified Water (PW), Water for Injection (WFI), or ultrapure water, depending on requirements.
- Control and Validation:
- Continuous monitoring and validation ensure the equipment is free of residues, contaminants, and microorganisms.
- Parameters like temperature, contact time, flow, and cleaning agent concentration are tightly controlled.
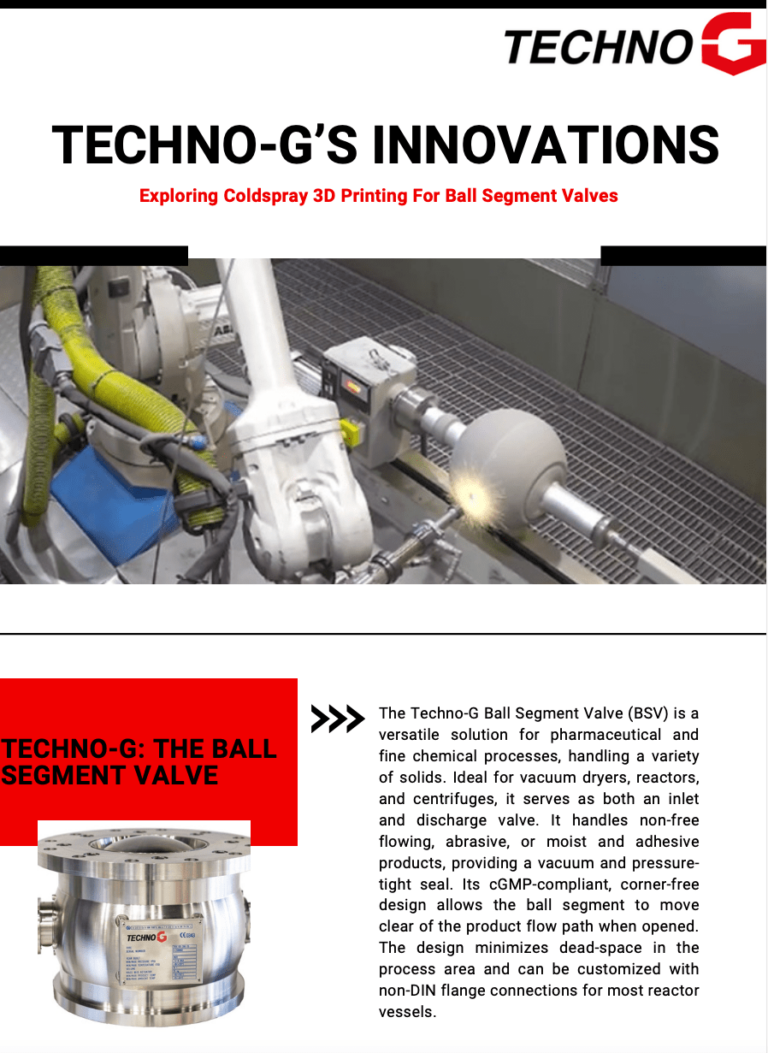
Download our free whitepaper
"Exploring Coldspray 3D Printing For Ball Segment Valves"
The Techno-G Ball Segment Valve (BSV) is a versatile solution for pharmaceutical and fine chemical processes, handling a variety of solids. Ideal for vacuum dryers, reactors, and centrifuges, it serves as both an inlet and discharge valve. It handles non-free flowing, abrasive, or moist and adhesive products, providing a vacuum and pressure- tight seal. Its cGMP-compliant, corner-free design allows the ball segment to move clear of the product flow path when opened. The design minimizes dead-space in the process area and can be customized with non-DIN flange connections for most reactor vessels.
The Techno-G Ball Segment Valve (BSV) is a versatile solution for pharmaceutical and fine chemical processes, handling a variety of solids. Ideal for vacuum dryers, reactors, and centrifuges, it serves as both an inlet and discharge valve. Learn more.
Advantages of CIP in the Pharmaceutical Industry:
- Efficiency: Saves time by eliminating the need to dismantle equipment.
- Consistency: Automation provides repeatable results.
- Hygiene and Safety: Reduces the risk of cross-contamination and complies with stringent GMP standards.
- Cost Savings: Optimized processes reduce the use of water, energy, and cleaning agents.
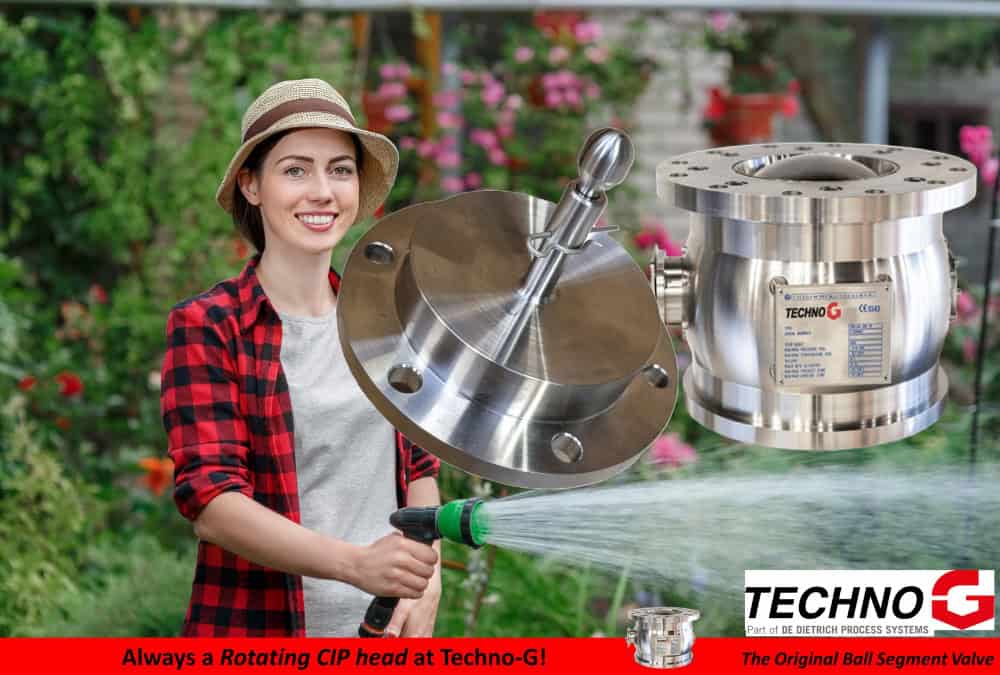
Additionally, Techno-G provides a unique CIP cover for the entire Ball Segment Valve Range, featuring a rotating CIP head that reaches all areas, including dead corners, ensuring comprehensive cleaning. Techno-G’s CIP cover is manufactured from stainless steel 316L, meeting high durability and hygiene standards. For more info: https://www.techno-g.com/ball-segment-valve/options/