Verständnis von Vakuumventilen und ihrer Bedeutung in industriellen Vakuumsystemen
tim2024-03-20T10:36:07+00:00Vacuum valves are components that are essential in a variety of industrial and research applications. They play an important role in creating and maintaining vacuum conditions. These valves, ranging from simple manual valves to complex automated systems, ensure precise control over the vacuum environment, essential for processes in industries like pharmaceuticals, food, cosmetics, and more. Let’s delve into the workings of vacuum valves and understand their significance.
Table of Contents
Understanding the vacuum valves first
A vacuum valve is a critical device that regulates the flow of gases or liquids in a vacuum system, integral to the vacuum chamber’s functionality. It’s designed to isolate and protect the system from atmospheric pressure while facilitating controlled conductance. The valve’s material, design, and seal types greatly influence its performance under various vacuum conditions. In these systems, vacuum valves are essential in maintaining stability and efficiency, ensuring that vacuum conditions are precisely maintained for applications ranging from scientific research to industrial manufacturing. By controlling exposure to atmospheric pressures and enabling exact vacuum modulation, these valves are indispensable in maintaining the integrity and functionality of the entire vacuum system.
Key components and functions
- Valve body: The main structure of the valve, often made from materials like stainless steel or aluminum alloys for durability and corrosion resistance.
- Valve seat and actuator: These parts work together to open or close the valve, controlling the flow within the vacuum system.
- Seals: From elastomer seals to more specialized options, the sealing mechanism ensures a tight closure, preventing air ingress that could disrupt vacuum conditions.
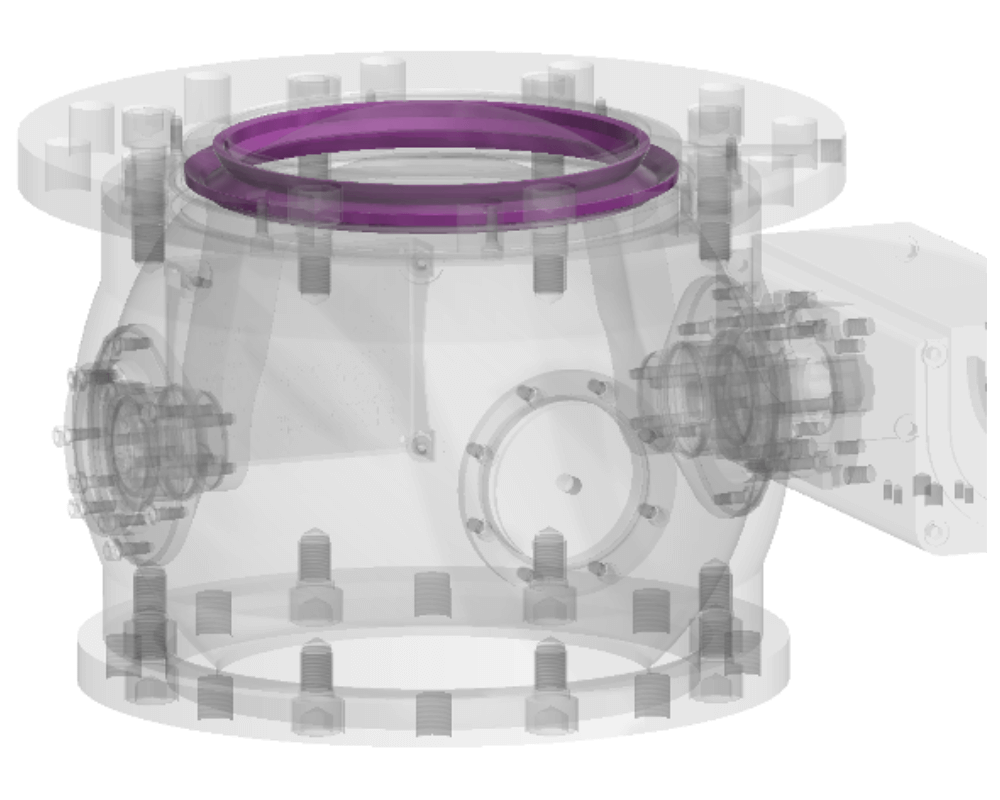
Conductance and flow control
Conductance in a vacuum valve refers to its ability to allow gas flow. Different types like butterfly valves or gate valves offer varying levels of conductance, suitable for different applications. Understanding the range of sizes and types of vacuum valves helps in selecting the right valve for specific vacuum applications.
SPEZIFIZIEREN SIE EIN TECHNO-G VENTIL FÜR IHRE ANWENDUNG
SPEZIFIZIEREN SIE EIN TECHNO-G VENTIL FÜR IHRE ANWENDUNG
Applications and Industries
Vacuum valves find extensive use in diverse industries, each with specific requirements. In the mentioned industries below, vacuum valves are primarily used to control and maintain vacuum conditions, rather than directly handling materials. For example:
- Pharmaceuticals: They’re essential in creating sterile environments and controlling pressure, essential for processes like lyophilization or sterile packaging.
- Chemicals: Vacuum valves play a role in safe containment and transfer of hazardous materials, often in processes requiring controlled atmospheres.
- Food and cosmetics: Here, they help maintain hygienic conditions, crucial in processes like vacuum packing or in maintaining cleanroom standards.
While these valves are vital in these sectors, their role is focused on managing vacuum conditions for process integrity and safety.
Vacuum valves vs. Ball segment valves
Vacuum- and ball segment valves serve different functions and are designed for distinct purposes:
- Vacuum valves: These valves are used to control gas flow within vacuum systems. Their primary function is to maintain and regulate vacuum conditions in a system, which is crucial in processes like semiconductor manufacturing, scientific research, and any application where a controlled vacuum environment is needed. They are not designed for handling solids but for controlling the pressure and flow of gases.
- Ball segment valves: Ball segment valves, on the other hand, are designed primarily for handling solids, particularly in industries like pharmaceuticals, food, and chemicals. They have a segmented spherical disc, which is fully shut-off by means of an inflatable seal that ensures 100% tightness and allows for precise control of material flow. They are known for their ability to handle abrasive or corrosive materials and are used in processes where there’s a need to control the flow of solid materials.
In essence, the key difference lies in their application: ball segment valves for solid material flow control, and vacuum valves for gas flow regulation in vacuum environments.
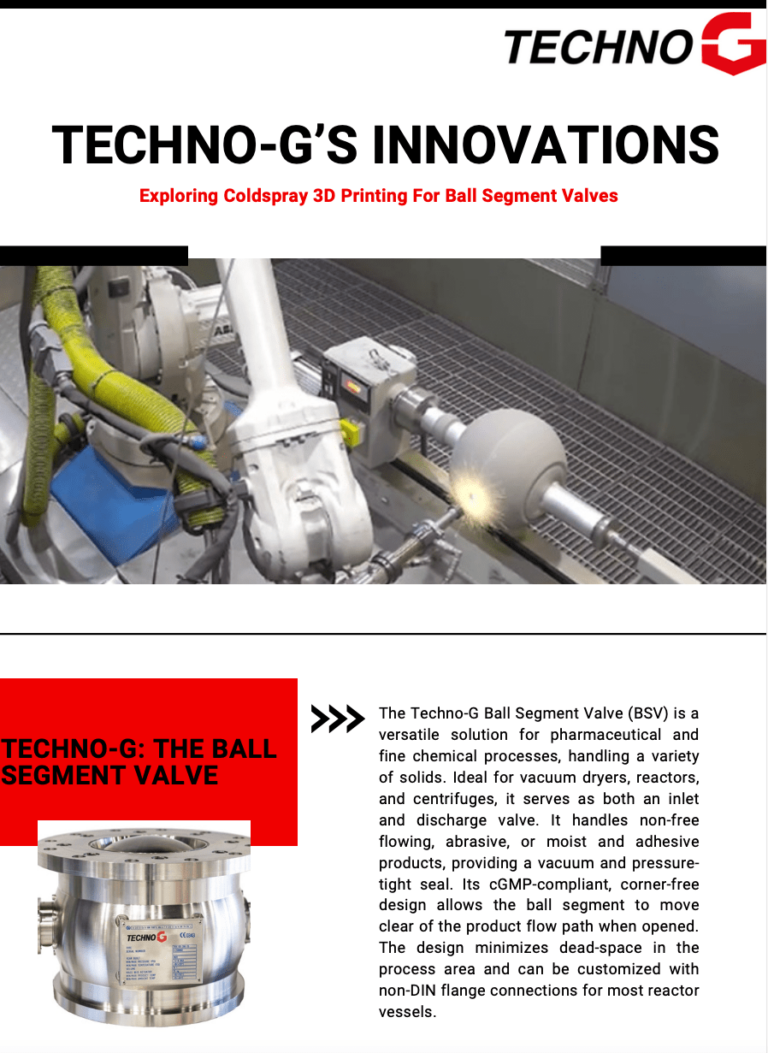
Laden Sie unser kostenloses Whitepaper herunter
"Erforschung des 3D-Drucks mit Kaltgasspritzen für Kugelsegmentventile"
Das Techno-G Kugelsegmentventil (BSV) ist eine vielseitige Lösung für pharmazeutische und feinchemische Prozesse, die eine Vielzahl von Feststoffen handhaben. Es ist ideal für Vakuumtrockner, Reaktoren und Zentrifugen und dient sowohl als Einlass- als auch als Auslassventil. Er verarbeitet nicht frei fließende, abrasive oder feuchte und klebrige Produkte und bietet eine vakuum- und druckdichte Abdichtung. Das cGMP-konforme, eckenfreie Design ermöglicht es dem Kugelsegment, sich beim Öffnen aus dem Produktflussweg zu entfernen. Die Konstruktion minimiert den Totraum im Prozessbereich und kann mit Nicht-DIN-Flanschanschlüssen für die meisten Reaktorbehälter angepasst werden.
Das Techno-G Kugelsegmentventil (BSV) ist eine vielseitige Lösung für pharmazeutische und feinchemische Prozesse, die eine Vielzahl von Feststoffen handhaben. Es ist ideal für Vakuumtrockner, Reaktoren und Zentrifugen und dient sowohl als Einlass- als auch als Auslassventil. Erfahren Sie mehr.
Are you looking for a valve for solid handling?
At Techno-G, we specialize in ball segment valves, a unique type of valve known for its precision and reliability. These valves are particularly effective for handling fine solid materials, equipped with a reliable inflatable seal for optimal pressure management.
We recognize the unique demands of each application. Our ball segment valves are designed with adjustable flow rates, various connection flanges, and compatibility with different pressure ranges and temperatures. We also offer custom executions for specific requirements.
Innovative sealing and material
- Alternative seal types: The seal is an important component. Advanced valves like Techno-G’s range feature inflatable seals in a wide variety of materials, which provide a 100%airtight closure, crucial for maintaining stable pressure conditions.
- Material choices: The choice of materials is essential for valve longevity and performance. Our valves are available in a variety of materials, including specialized options like 3D cold spray printed titanium, offering unparalleled strength and corrosion resistance.
Integration with control systems
Our ball segment valves can integrate with control systems for automated operation, essential in industries requiring precise control. They are compatible with various pressure sensors for real-time monitoring.
WENDEN SIE SICH AN UNSER EXPERTENTEAM FÜR IHRE ANFRAGEN
Applications in specialized industries
Our valves are used across multiple industries, each with its unique challenges.
- Pharmaceuticals and chemicals: Our valves meet stringent safety and hygiene standards, ensuring secure and contamination-free handling.
- Metals and minerals: Designed to manage abrasive materials efficiently in industries like metals and minerals.